Powder Metallurgy Solutions for Electric Vehicles
The electric vehicle market has been experiencing tremendous growth, which has increased the need for lightweight, efficient, and high-performance metal components. Powder metallurgy (PM) is capable of producing intricate parts that meet the unique performance needs of electric vehicles. Unlike conventional manufacturing methods, powder metallurgy offers greater control over a product’s physical characteristics and can produce highly detailed components with complex geometries.
At Allied Sinterings, we’ve been delivering custom-engineered powdered metal components for over 65 years, including EV sintered parts. Below, you can learn more about how the PM process works for EV components, the benefits you can expect, and more.
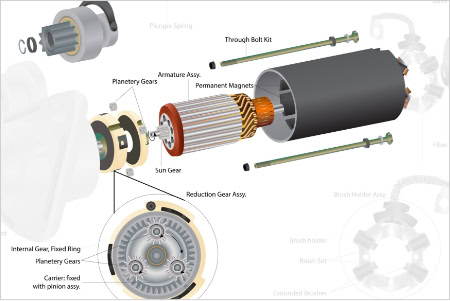
Introduction to Powder Metallurgy for Electric Vehicle Components
Powder metallurgy is the process of transforming powdered metal materials into a high-precision component. The manufacturing method involves compacting metal powders into the desired shape and then heating them just below their melting point, a technique known as sintering. Unlike other manufacturing options, PM provides more control over material composition, porosity, and complexity, making it a well-suited process for electric vehicle applications.
For the EV industry, one major benefit of the PM process is its efficient use of materials. Powder metallurgy only uses the precise amount of metal powder that is needed to manufacture each component, minimizing production costs, waste, and environmental impact. Not only does the process align with sustainability goals, but it also meets the EV industry’s need for high-volume durable parts in energy-efficient, lightweight designs.
Benefits of Powdered Metal Components in EVs
PM components are essential to EV technology. Allied Sintering’s powder metallurgy capabilities offer numerous benefits for EV parts:
Weight reduction is one of the most critical factors of EV efficiency. PM is an effective method of minimizing component weight without sacrificing strength. This helps to extend the driving range of EVs while reducing energy consumption.
PM facilitates the mass production of intricate EV components with minimal raw material waste. It also achieves near-net shapes, resulting in components that come out of the mold ready for use, with little need for post-processing techniques. Combined, these factors significantly reduce manufacturing costs compared to traditional manufacturing methods.
Powdered metal components can be engineered to handle the high temperatures and continuous mechanical stress that is common in EV powertrains. This results in improved reliability and durability, even under challenging operating conditions.
Applications of Powdered Metal Parts in EVs
At Allied Sinterings, we can produce powdered metal parts for the following EV applications:
Electric Vehicle Success Story
Allied Sinterings has a long history of solving EV industry challenges. The following case study demonstrates our ability to create extremely tight tolerance parts that adhere to demanding performance specifications.
Realizing a Pinion Gear Design with Extremely Tight Tolerances
An automotive client approached us with a challenge they were facing manufacturing a pinion gear. Their gear design featured unusually tight tolerances for inner diameter (ID). While most small powdered metal components feature an inner diameter of ± 5/10ths, the client required an even tighter tolerance to fit the motor shaft of their electric vehicles. The part, specifically a “press fit” pinion, had to be small enough to fit onto the shaft and tight enough to not slip.
Achieving 7/10ths of a Typical Tolerance for an ID
With over 10 million automotive industry components sintered annually, our team is highly experienced in meeting challenges like this. We use specialized tight tool maintenance and process control techniques to achieve extremely tight tolerances. For this project, we first confirmed the client’s performance requirements and then selected the correct raw materials before beginning the powder metallurgy process.
The result was a finished component that did not require any resizing using drilling, reaming, or ballizing techniques. We held a ± 3.5/10ths tolerance on a press fit ID for a total of 7/10ths tolerance. Our customer was completely satisfied with the end product.
View the full case study here for more details.
Partner with Allied Sinterings for High-Quality Small & Miniature Powdered Metal Components
Powder metallurgy offers a cost-effective, reliable way to meet the EV industry’s strict requirements for lightweight, high-performance components. At Allied Sinterings, we are a recognized world leader in custom manufacturing small and miniature powdered metal parts for electric vehicles and various other applications in many industries. Whether you need EV sintered parts for motors, battery systems, or otherwise, our experts can deliver tight tolerances and premium quality.
Allied Sinterings is ISO 9001:2015 certified and uses lean manufacturing techniques to ensure you always get the best value. Every effort is made to provide our customers with the best results possible by producing high-quality components that meet their design specifications with dimensional and repetitive accuracy. Our processes are fast and reliable. If you need PM components for your EV project, contact us today.